ANTARABANGSA
Proses Pemasangan Honda City Generasi Baharu Berbeza Berbanding Sebelum Ini
Sejak 2003, kebanyakkan model-model Honda yang dijual bagi pasaran Malaysia adalah kenderaan yang melakukan pemasangan tempatan (CKD).
Dengan ada kenderaan CKD yang dipasang di Pegoh, Alor Gajah, Melaka, barulah kita boleh nampak lebih banyak kenderaan jenama Honda berada di jalan raya Malaysia. Ini kerana, harga yang ditawarkan agak kompetitif dan mampu milik berbanding model CBU.
Sebagai contoh, Honda Jazz yang sebelum ini diimport dari Jepun yang dijual lebih RM100,000, tetapi bagi model CBU ia dijual lebih rendah dan lebih ramai mampu untuk memilikinya.
Kini, kilang Honda di Pagoh yang mempunyai dua saluran produksi untuk menghasilkan model Jazz, Jazz Hybrid, City, City Hybrid, Civic, BR-V, HR-V, HR-V Hybrid, CR-V dan Accord. Kapasiti kilang itu mampu menghasilkan 100,000 kenderaan setahun.
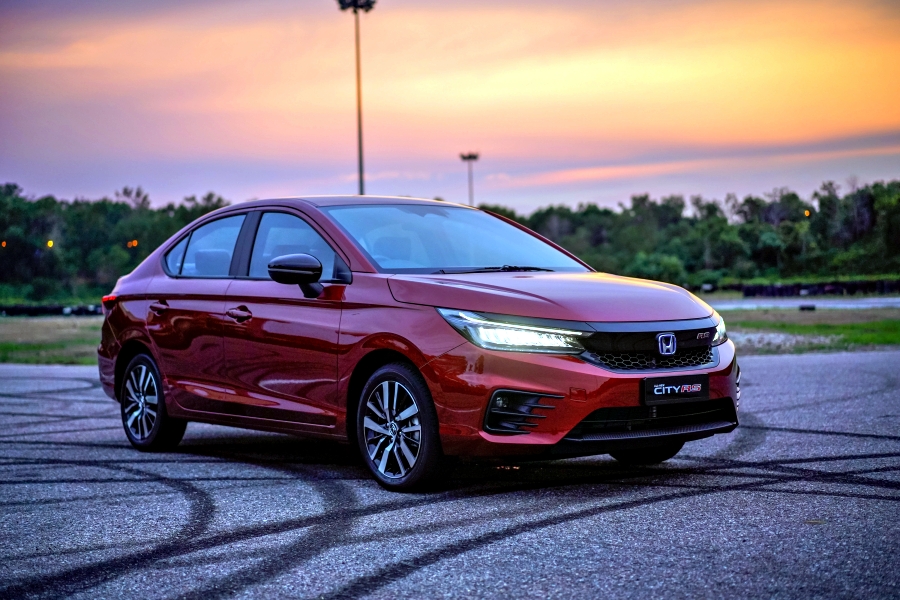
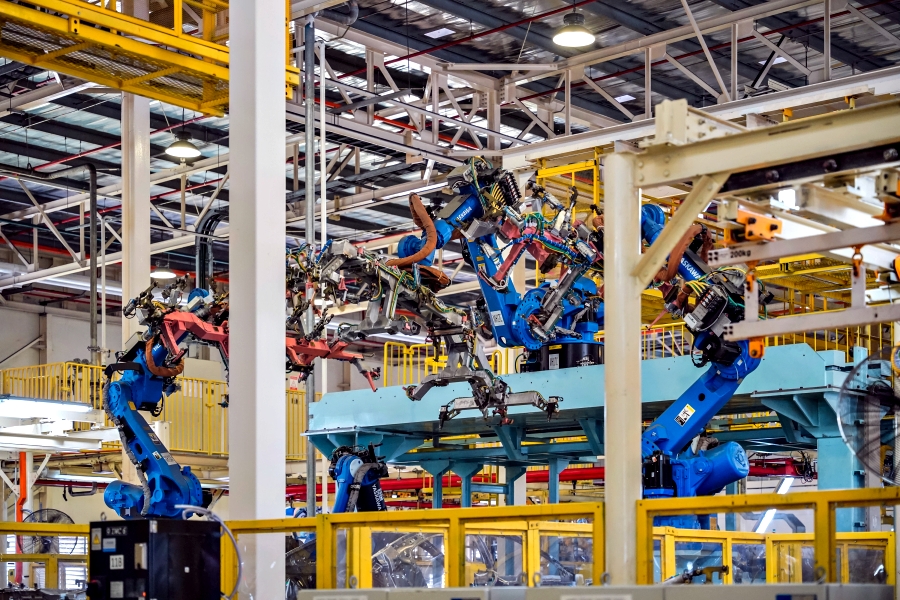
Dalam pemasangan City generasi baharu ini, ada lagi satu proses tambahan yang dipanggil Inner Frame. Proses ini, kerangka sisi dalaman dan bawah dicantum terlebih dahulu sebelum mencantumkan kerangka lain.
Proses tambahan itu bertujuan untuk memberi lebih ketegaran kepada kerangka, sekali gus mampu membuatkan pengendalian kenderaan lebih stabil.
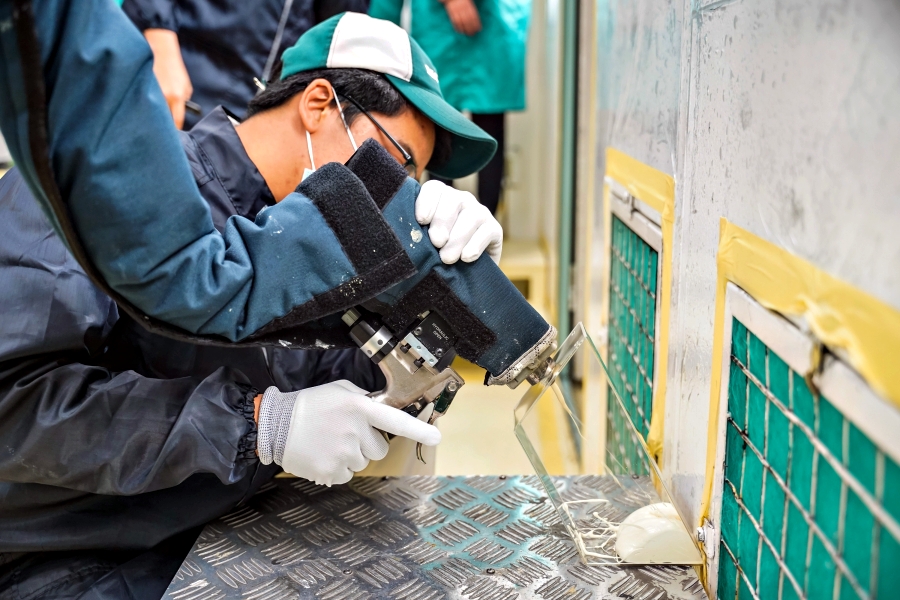
Sebelum ini, ia diletak dengan span, tetapi dengan penggunaan Spray Form ia mampu mengurangkan NVH sehingga 33 peratus.
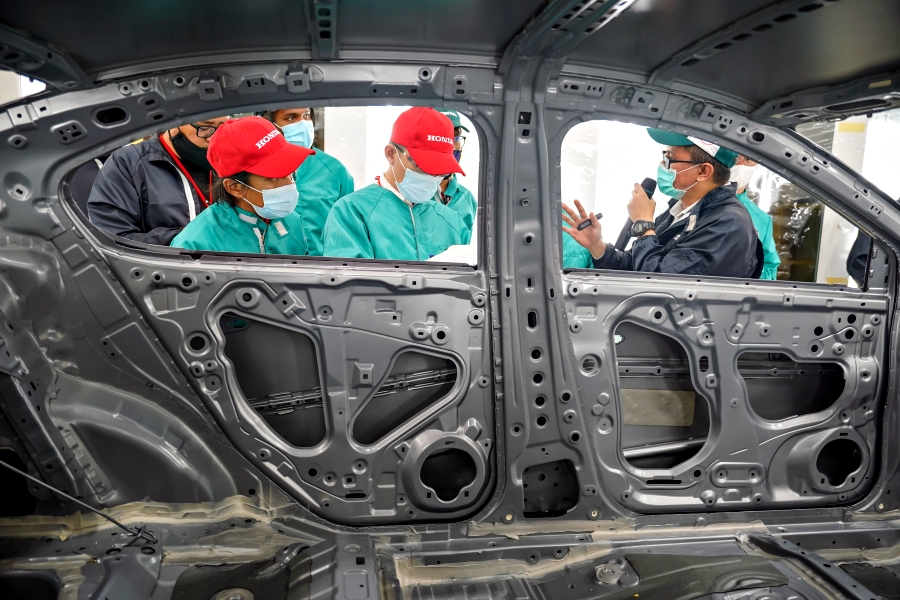
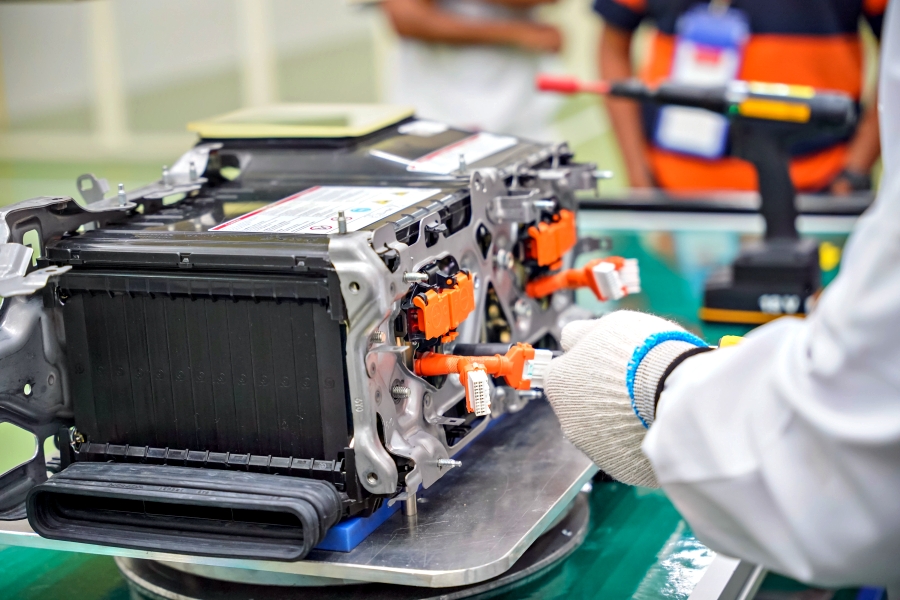
Memandangkan Honda adalah model paling banyak menawarkan segmen hibrid di negara ini termasuk City RS, sudah pasti mereka memerlukan jumlah bateri litium-ion yang banyak untuk memenuhi keperluan kilang pemasangannya.
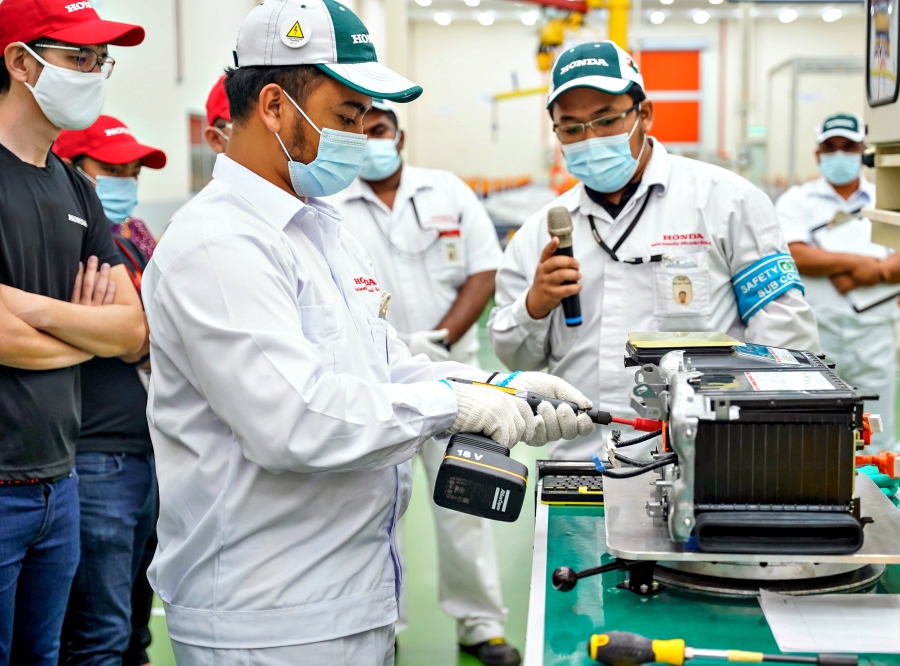
Bateri litium-ion terbabit dibekalkan daripada syarikat Panasonic dan Blue Energy, selain proses pemasangan IPU itu mengikut piawaian Honda Jepun untuk menjamin kualitinya.
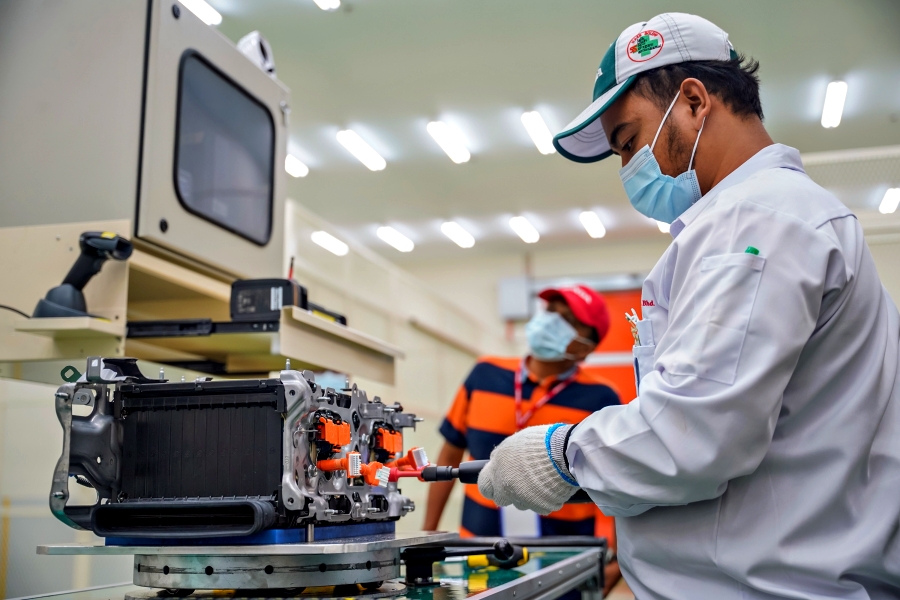
Must-Watch Video